If you’re planning to set up a new warehouse, or expand into storage and distribution, efficiency is everything. You need to get goods in and stored efficiently, track and stack goods efficiently and ship goods out efficiently to be profitable.
The smoother the operation, the more you get done, the happier your customers are and the more money you’ll make.
While setting up a warehouse is a huge undertaking, we’re going to discuss one small part of that.
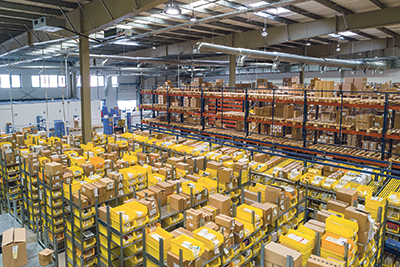
Storage efficiency
Storage efficiency not only helps you store more goods within a finite space, it can also make that space safer for staff.
Moving, storing, stacking and removing goods are all made safer when you do it right.
Here are some ideas to help improve efficiency within a warehouse. Use one, use them all, it’s entirely up to you!
Design the flow
If you’re setting up a new warehouse, you can design it from the ground up for maximum efficiency. That’s great as you won’t have to retrofit a smooth flow into your operations.
Draw a layout of the warehouse including receiving and dispatch. Then draw a line between where goods enter and where they leave.
Place storage somewhere close to that line to minimise movement and speed up the transfer.
Place popular items close to that line
Every warehouse has fast movers and slow movers. A fast mover is a product that goes out as quickly as it comes in. A slow mover may sit in your warehouse for a while before being dispatched.
Ideally, you want fast movers close to that line you drew between receiving and dispatch.
Make sure they are easily accessible and can be moved and loaded with minimum stress.
Slow movers can be placed elsewhere along the line to fill up space.
Ask staff for ideas
If you’re working in an established warehouse or have employed experienced staff to help set up, use that experience to help.
There are always dark corners in a warehouse or areas where the light doesn’t travel as far as it should. Areas that look good on paper but don’t work in practice.
Experienced warehouse hands can help you avoid those.
Understand the goods you’ll be working with
You will likely store and transport goods of all shapes and sizes. However, having an idea ahead of time allows you to design your flow, storage solutions and processes around the most common type of item you’ll deal with.
You can optimise storage for the size, shape and type of item and hopefully see efficiencies as a result.
Use the right shelving or storage medium
Not all warehouse storage is created equal or will be suitable for all types of goods. That’s why knowing in advance (as much as possible) what type of good you’ll be handling is useful.
Select the right storage for the right situation and you’ll be efficient.
Use pallets for heavier or bulk items, shelves for smaller items or for height efficiency, use bins or racks for suitable items and so on.
Use the right containers
Once you have an idea of the goods you’ll be working with, source the right container for the job.
Use Euro stacking containers for maximum flexibility and standard sizing. They fit onto pallets, dollies and forklifts and come with handles for safe handling.
They can stack efficiently when full or empty and fit snugly into trucks. Some will nest when empty for even more space efficiency.
Set up a work in progress area close to dispatch
The vast majority of goods will flow in, be stacked and flow out in the same form. Others will need to be broken down, picked and packed.
This requires a WIP, or Work In Progress, station. A safe area where staff can pick and pack orders and assemble them outside the flow of goods, but close enough to be efficient.
The size of that area will depend on how much you’ll be breaking open pallets and picking and packing orders.
The more you envisage doing that, the larger your WIP area should be.
Store similar items together
If you deal with multiple versions of similar items, place them together in storage. That way, if staff can find one type of the item, it won’t take them long to find the specific item.
This requires more care on the part of staff to avoid picking the wrong version but helps them too.
If they can find one type of widget, they know the widget they are looking for will be close by.
Group commonly shipped items close together
If you find you’re shipping multiple items together frequently, don’t be afraid to reorganise the warehouse so they are close together.
That way, pickers can work their way along an aisle or area picking an entire order with minimal walking or getting in the way of loading or forklifts.
Design clear labelling
Warehouse labelling is almost as important as shelving and the containers you use. Without a clear, coherent system that can work with your IT, you’re not going to be efficient.
Use best practices for labelling, managing SKUs and product identification. There is no one ‘perfect’ way. Find the method that works for you and your team and stick with it.
Setting up a warehouse can be a daunting task but you have the advantage of being able to build in efficiency and technology from the very beginning.
It’s an exciting opportunity and one we wish you all the best with!
T 01628 829800
enquiries@plastor.co.uk
https://www.plastor.co.uk